Faster from order to cash
CHALLENGE
Global chemicals company
- Supplies products to a wide range of industries: raw materials, additives and process aids.
- The various global operations coordinated their own Order-to-Cash efforts, which led to processes looking very different.
Create an overview of the all the Order-to-Cash processes:
- Map the different process variants.
- Identify the root causes for difference in lead time between different processes.
APPROACH
- The actual Order-to-Cash processes from each of the regions were visualised with process mining. This included all the variants of each of the processes. The event logs from the ERP systems were used.
- From various viewpoints (cycle time, performance, organisation) the processes were analysed:
- For the various bottlenecks and rework loops, root causes were identified.
- In a next step the best practices were used to improve each of the processes.
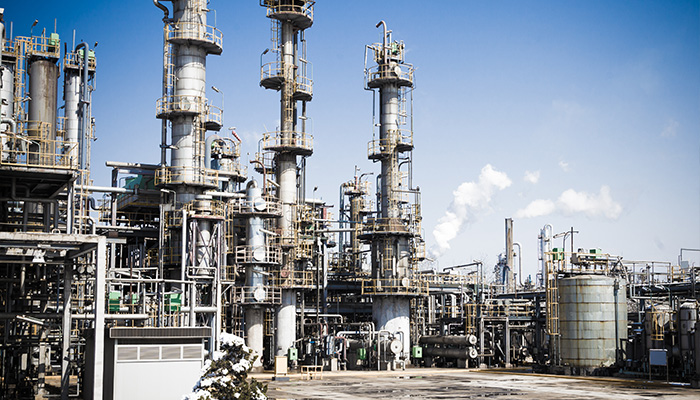
Significant reduction of the Order-to-Cash lead time.
Redesigned and more harmonised processes across the various operations.
Improved KPIs that are used in the reporting structure.
Clear identification of best practices that fed shared learning between the various operations.