Smarter production line planning lets you respond to changes in customer demand and improve your margins
CHALLENGE
A process manufacturer with a network of assets spread across Europe needed to respond more flexibly to changes in customer demand while maintaining high asset utilisation, low working capital and low transport costs.
The situation was complex. The assets were different and had their own characteristics. The outflow from the installations could not simply be stopped between production runs, and a change of material resulted in a massive production loss – although a product type change without a change of material was doable.
The producer had 25 production lines and served 1,000 customers with a total of 2,500 products. In short, the perfect complex planning issue for which our More Optimal platform was designed.
APPROACH
The planners had been working with a combination of SAP and Excel spreadsheets. They were handling a huge number of variables and attempting to incorporate increasingly shorter delivery times. The planners understood their trade, but the complexity of the puzzle was too great for the resources available. There was much to gain.
Our generic More Optimal platform makes it possible to create a customer-specific application in a short time, with all relevant planning rules built in. The platform is set up in close consultation with the user. First, the relevant Key Performance Indicators (KPIs) were defined. These included (1) demand fulfilment, (2) asset pull / productivity, (3) inventory, (4) transport costs and (5) planning effort.
In a number of joint work sessions, we established the planning process and drew up the rules for allocating products to the various production lines. In addition, the transport options relating to production locations and the rules for product changes were built in. By working closely with the planners at every step, we gradually developed the More Optimal platform, and this now shows in real-time the consequences of the decisions made by the planners and gives advice on how to improve the planning process.
The application is also used to evaluate what-if scenarios and their impact on the KPIs. The manufacturer uses this functionality as part of the annual planning and budgeting process and relies on it for concrete operational issues on a more regular basis.
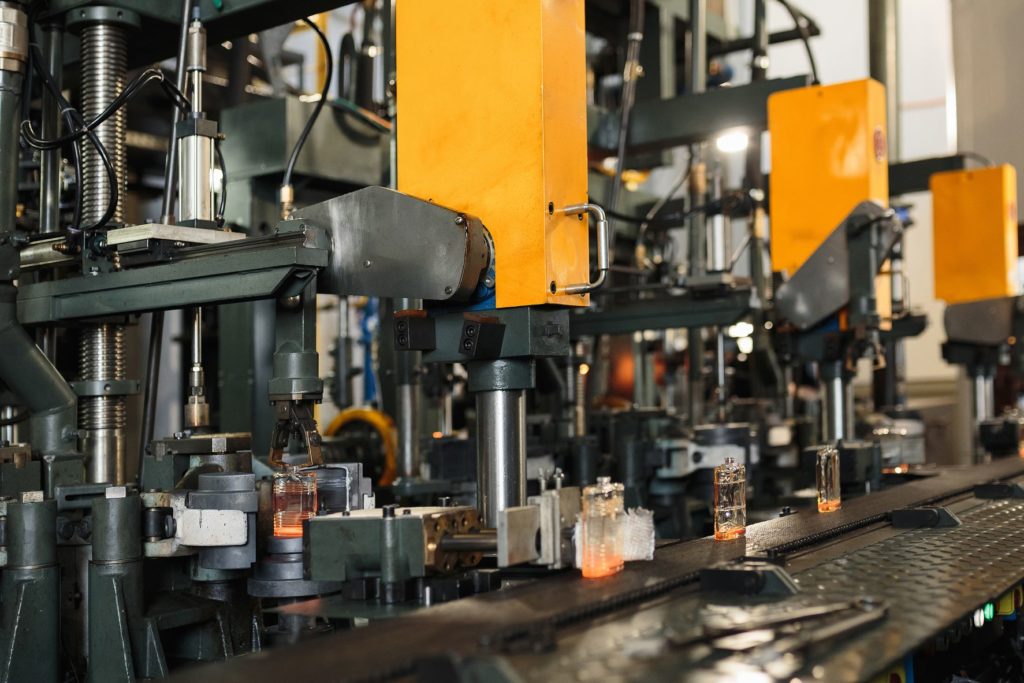